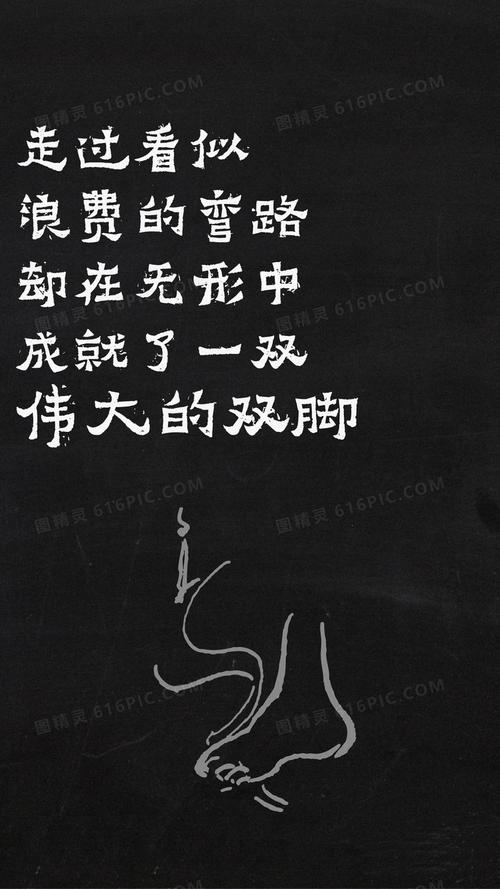
课 程 设 计
题 目 | 电阻炉微型计算机温度控制系统的设计 |
学 院 | 自动化 |
专 业 | 自动化 |
班 级 | 1103 |
姓 名 | 萨楚拉 |
指导教师 | 张素文 |
| |
课程设计任务书
学生姓名: 萨楚拉 专业班级: 自动化1103
指导教师: 张素文 工作单位: 自动化
题 目: 电阻炉微型计算机温度控制系统的设计
初始条件:
设计一个电阻炉微型计算机温度控制系统,系统为一阶惯性纯滞后特性(参数自定),温度控制要求为500℃,温度控制精度为 1℃;通过LED 显示温度;
要求完成的主要任务:
1. 输入通道及输出通道设计;
2. LED接口设计;
3. 采用改进PID控制算法;
1. 系统软件流程及各程序模块设计并用仿真软件演示;
4. 完成符合要求的设计说明书。
时间安排:2013年6月25日~2013年7月4日
指导教师签名: 年 月 日
系主任(或责任教师)签名: 年 月 日
目录
1 控制对象 1
1.1控制对象介绍 1
1.2 控制性能要求 1
2方案的比较和确定 1
3统软硬件设计 2
3.1总体设计 2
3.2温度检测电路 3
3.3 控制信号输出通道 3
3.4 LED显示电路 4
4 系统软件设计 5
4.1 程序流程图 5
4.2控制算法 6
5基MATLAB仿真被控对象 8
6.心得体会 10
参考文献 11
附录一 电路图 12
附录二 程序代码 13
摘要
当今社会,随着产品的精细化,温度对产品的影响原来越受到人们的关注,于是,温度控制成为了工业生产中重要的控制参数之一。这样,一个能够精确控制温度的系统成为人们迫切的需要,它将能够广泛的被使用于的各种加热炉、精密器件制造、甚至于食品行业等。
本次试验便以电阻炉的温度控制为例,试图探求一个具有良好稳定性的温度控制系统。本次试验以C51单片机为核心,采用温度变送器桥路和固态继电器控温电路,该控制系统具有硬件成本低、控温精度较高、可靠性好、抗干扰能力强等特点。基本的想法是:C51单片机能够按要求对电阻炉进行实时监测和控制算法的确定,发出准确的控制命令;A/D转换芯片将得到的模拟量转化为数字量;单片机对数字量进行处理,得到应有的控制量,去
控制加热功率,从而实现对温度的控制。
关键词:单片机、电阻炉、温度测量、控制系统
电阻炉微型计算机温度控制系统的设计
1 控制对象
1.1控制对象介绍
电阻炉是利用电流通过电热体元件将电能转化为热能来加热或者熔化工件和物料的热加工设备。
电阻炉由炉体、电气控制系统和辅助系统组成。炉体由炉壳、加热器、炉衬(包括隔热屏)等部件组成。电气控制系统包括电子线路、微机控制、仪表显示及电气部件等。辅助系统通常指传动系统、真空系统、冷却系统等,虽炉种的不同而已。
电阻炉的主要参数由额定电压、额定功率、额定温度、工作空间尺寸。生产率、空炉损耗功率、空炉升温时间、炉温控制精度及炉温均匀性等
1.2 控制性能要求
本设计要求控制一个电阻炉,它是一个具有很大滞后性的系统,惯性也很大,其传递函数的形式可以写为,温度控制要求为500℃,温度控制精度为 1℃,电阻炉的温度还要通过LED 实时显示出来。
2方案的比较和确定
方案一
系统采用8084芯片作为系统的微处理器。温度信号由热电偶检测后转换为电信号经过预处理(放大)送到A/D转换器,转换后的数字信号再送到8084芯片内部进行判断或计算。从而输出的控制信号来控制锅炉是否加热。但对于8084芯片来说,其内部只有128个字节的RAM,没有程序存储器,并且系统的程序很多,要完成键盘、显示等功能就必须对8084芯
片进行存储器扩展和I/O口扩展,并且需要容量较大的程序存储器,外扩时占用的I/O口较多,使系统的设计复杂化。
方案二
系统采用AT89C51作为系统的微处理器来完成对炉温的控制和键盘显示功能。C51单片机片内除了128KB的RAM外,片内又集成了4KB的ROM作为程序存储器,是一个程序不超过4K字节的小系统。系统程序较多时,只需要外扩一个容量较小的程序存储器,占用的I/O口减少,同时也为键盘、显示等功能的设计提供了硬件资源,简化了设计,降低了成本。因此89C51可以完成设计要求。
综上所述的二种方案,该设计选用方案二比较合适。
3统软硬件设计
3.1总体设计
系统的硬件包括微控制器部分(主机)、温度检测、温度控制、人机对话(键盘/显示)4个主要部分,系统的结构框图如图3-1所示。
系统程序采用模块化设计方法,程序有主程序、中断服务子程序和各功能模块程序组成,各功能模块可直接调用。
图3-1系统结构框图
3.2温度检测电路
温度检测电路包括温度检测电路、放大器和A/D转换三部分。原理图如图3-2所示
图3-2温度检测电路
Pt100温度传感器的测量范围为:,符合题目中的温度测量。它是利用金属铂在温度变化时自身电阻值也随之改变的特性来测量温度的,显示仪表将会指示出铂电阻的电阻值所对应的温度值。当被测介质中存在温度梯度时,测得的温度是感温元件所在范围内介质层中的平均温度。
铂电阻的阻值随温度的变化而变化的计算公式:
-200<t<0℃ Rt=R0[1+At+Bt+C(t-100)t] (3-1)
0<t<850℃ Rt=R0(1+At+Bt2) (3-2)
Rt为t℃时的电阻值,R0为0℃时的阻值。公式中的A,B,系数为实验测定。这里给出标准的系数:A=3.90802*10-3℃;B=-5.802*10-7℃; C=-4.27350*10-12℃。
3.3 控制信号输出通道
该电路用到了芯片MOC3021,它是过零触发双硅输出光耦。过零触发是在设定时间间隔内,
改变晶闸管导通的周波数来实现电压或功率的控制。 实际上它就相当于一个用于交流电路中的“电子开关”,这个电子开关的“接通”、“断开”动作是在交流电流过“0”点完成的。这样的电路,对用电负荷不会造成“电流冲击”。电路的工作状况是“断续”的,适用于本系统热惯性较大的电阻炉负载。
控制信号输出通道的电路图如图10所示,考虑到加热系统具有较大的热惯性,即一阶惯性纯滞后特性,本系统采用脉冲宽度调制(PWM)的控制方法,单片机输出控温信号。单片机输出低电平时,使双向可控硅导通,电热丝通电;输出高电平时,双向可控硅截止,电热丝断电。其中,7407用于驱动,提供更大的电流驱动发光二极管。可控硅门极回路与220V电源相通,光电耦合器有效地把单片机系统与220V强电隔离,确保了单片机系统的安全性。原理图如3-3所示
图3-3控制信号输出通道
3.4 LED显示电路
由于温度控制精度为1℃,设计中选取型号为7SEG-MPX4-CC的数码管显示器,其为共阴极数码管。工作方式为动态显示方式。动态显示,就是微型机定时地对显示器件扫描,在这种方法中,显示器件分时工作,每次只能一个器件显示。但由于人视觉的暂留现象,所以,仍感觉所有的器件都在显示。
图3-4LED显示电路
4 系统软件设计
4.1 程序流程图
该控制系统的流程图如图4-1所示,首先对单片机的各个控制端口以及各个参数初始化,然后就启动A/D转换,读取转换后的数据。对转换后的数据进行滤波等操作,使数据的准确性提高,然后进行标度变换,得到实际的测量温度。把测量温度进行处理后送到数码管显示,把测量温度与规定温度作比较,判断是否动作。同时计算测量温度与标准值之间的偏差,根据偏差判断是进行PID计算还是积分项改进(分离)的PD计算,得到PWM脉冲控制执行机构,然后程序重复执行。
图4-1电阻炉系统控制流程图
4.2控制算法
4.2.1控制算法的确定
PID调节是连续系统中技术最成熟的、应用最广泛的一种控制算方法。它结构灵活,不仅可以用常规的PID调节,而且可以根据系统的要求进行改进,适时的采用各种PID的变型,如PI、PD控制等,本次试验便是使用改进的PID控制算法,它具有许多特点,如不需要求出数学模型、控制效果好、能够避免积分饱和、能够消除积分不灵敏区等,特别是在温度调节系统中,由于被控量变化较为缓慢且有惯性和滞后情况,积分项往往会产生很大的积累,导致系统产生很大超调,甚至发生震荡,使用改进PID控制算法可以将积分项进行分离,提高系统稳定性。改进PID控制系统的结构框图如图4-2所示:
图4-2 系统结构框图
具有一阶惯性纯滞后特性的电阻炉系统,其数学模型可表示为:
(4-1)
在改进PID调节中,需要根据多次测试确定积分分离阈值β,当时,采用PD控制,当时,采用PID控制。阈值β一定要选取合适,若选取过大,达不到积分分离的目的,若选取过小,被控量无法跳出积分分离区,一直处于PD控制,将会出现残差。确定β时,可以先假设一个值,然后测试若干个不同的PI、PD参数,得出一组较好的控制参数。积分分离控制算法可表示为: