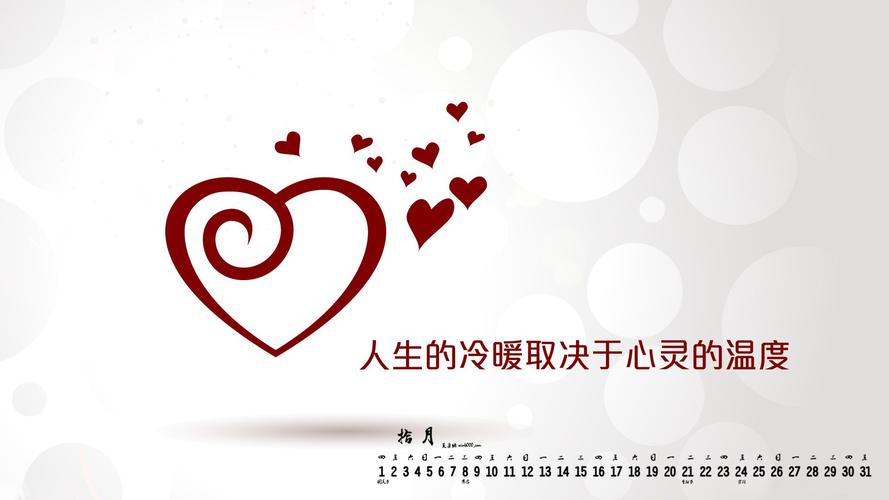
CFB锅炉高温过热器改造
摘要:阐述新一代CFB锅炉高温过热器特点以及频繁出现泄漏情况;分析发生泄漏的原因,提出解决泄漏的办法并进行优化。
关键词:高温过热器:锅炉;CFB;TP347H;泄漏
一、引言
华南地区某电厂3×350MW超临界机组,并入局域网运行,主要向电解铝供电、氧化铝供高低压抽汽,三台锅炉型号为DG1242/25.4-II1,是东方锅炉股份有限公司自主设计开发的第三代超临界CFB锅炉。锅炉采用单布风板、单炉膛、M型布置、平衡通风、一次中间再热、循环流化床燃烧方式,采用高温冷却式旋风分离器进行气固分离,锅炉整体支吊在锅炉钢架上。
高温过热器共12片,布置在炉膛上部靠近炉膛前墙且在锅炉左右方向上均匀布置,过热器为膜式结构。12片管屏采用并联布置,即过热蒸汽在管屏内由下向上流动至高温过热器出口集箱,整个高温过热器自下向上膨胀。高温过热器单屏24根,管子规格Φ63.5×11.5,材质SA-2
13T91/SA-213TP347H,材料分界点标高为41.61米,靠出口端有材质为SA-213T91的散管过渡,屏宽1.75米,屏间距为0.6米。该发电厂3台超临界循环流化床机组并入局域网,满足轻合金用电的同时向氧化铝厂提供高、低压蒸汽,电、汽都不能中断,因此对机组的安全可靠性要求特别高。
该电厂1号机组自2017年12月27日投产以来(2号机组2018年2月12日投产、3号机组2018年5月3日投产),机组运行时间不长,1号锅炉高温过热器先后泄漏4次,3号锅炉高温过热器泄漏1次,给发电厂、公司的安全生产带来巨大的不利局面,高温过热器改造尤为必要。
二、问题现状
发电厂投产以来锅炉高温过热器泄漏具体情况如下:
⑴2018年2月4日,1号锅炉高温过热器首次泄漏,首爆管:炉右数高过第12屏第9根管,标高约51.6m。经过18天抢修,机组于2月24日并网。
⑵2018年2月27日,1号锅炉高温过热器第二次泄漏,首爆管:高温过热器右起第5排第17
根,标高约51m。经过32天抢修,机组于4月1日并网。
⑶2018年4月4日,1号锅炉高温过热器第三次泄漏,首爆管:高过第五屏第9根管子泄漏,标高约58m。经过69天抢修,机组于6月13日并网。
⑷2018年7月12日,1号锅炉高温过热器第四次泄漏,首爆管:高温过热器第7排23根管泄漏,标高51m。经过6天抢修,机组于月日并网。
⑸2018年6月23日,3号锅炉高温过热器第一次泄漏,首爆口:第2屏高过第22根管子泄漏,标高约51.8米。经过52天抢修,机组于8月16日并网。
三、原因分析
发生泄漏后,第一时间通知东方锅炉厂专家、科研院所专家到现场,分析泄漏原因,制定抢修方案。另在机组检修过程中,对3台锅炉未泄漏部位的膜式壁高温过热器标高41.2-61米进行打磨、PT检验,发现鳍片间的管子存在大量横向裂纹(见图1)。
图1 高温过热器横向裂纹
2018年7月,邀请多名国内锅炉厂、高等院校、电力研究院等知名循环流化床锅炉、材料等方面专家,对奥氏体耐热钢膜式壁裂纹进行分析、探讨。
高过膜式壁管屏选用的材料为TP347H,属于奥氏体不锈钢,是成熟钢种,在煤粉炉高温高压受热面已有多年使用历史,TP347H具有优良的抗晶间腐蚀性能,较高的持久强度、良好的组织稳定性和抗氧化性能,此外还具有良好的弯管和焊接性能。但是,TP347H热膨胀系数高(是普通钢材的1.5倍)、导热性差;由于铌元素(Nb)的添加,目的是固化碳元素,提高材料的持久性能、抗高温氧化性能,但是在高温下(大概500-1050℃区间),含Nb不锈钢会快速析出NbC,这本身也是设计TP347H钢种的强化原理之一。焊接时,紧临熔合线的区域会形成二次固溶作用,晶粒粗化,稍远的区域则产生轻度NbC的析出(时间短),即形成通常所说的热影响区。在较长时间的高温运行下,热影响区将因NbC相对快速而持续的析出形成低塑性区,且存在晶内析出强化晶粒、晶界析出弱化晶界的情况,当应力足够大时,易萌生沿晶裂纹(见图2)。
图2 高温过热器沿晶裂纹显微组织
高温过热器膜式结构的特殊性决定了同管屏间管子的温差是不可避免的,高温过热器管屏在炉膛内高度达到30余米,且不锈钢膨胀系数比较大,由于在炉膛里吸热不均匀、管子内蒸汽流量不均匀、管子之间鳍片冷却慢等,造成同一管屏里管子间存在温差,在膜式结构下形成较大轴向应力,造成管子撕裂。
低塑形裂纹的影响区域有大有小,与焊接应力、温差引起的应力有关,这也就是有的部位有裂纹,有的部位没有裂纹。
四、方案实施
图3 高温过热器改造安装图
考虑到局域网对机组的安全可靠性要求特别高,每次非计划停运,造成的直接损失、间接损失非常巨大,结合国内专家的意见,历经几次抢修不同改造,最终方案是将3台锅炉标高41.2-61米的膜式壁高温过热器改为光管高温过热器,仍采用TP347H,并安装五层套管,防止其变形(见图3、图4)。
图4 高温过热器改造现场图
1.1号锅炉:
⑴1号锅炉高过第1次泄漏后,对所有受损管进行更换,即“哪有问题处理哪儿”。
⑵1号锅炉高过第2次泄漏后,更换标高51.8米工地焊口上下各2米区域的管屏,单片屏24根管子,共计12屏。更换后的管子之间不补焊扁钢;原管屏上扁钢端部进行绕焊;管间扁钢端部增开止裂缝。现场填充扁钢和制造扁钢交接位置全部切掉更换,消除扁钢回填带来的问题。
⑶1号锅炉高过第3次泄漏后,更换标高53.4—61.6米区域的管屏,单片屏24根管子,共计12屏,分为6个管组,每个管组由4根管子组屏;更换标高49.8—41.91米区域的管屏,单片屏24根管子,共计12屏,下部单屏分为5个管组,每个管组由4根或6根管子组屏,将屏的宽度进一步缩小,减小同屏管之间的应力。
⑷虽然将大屏改成了小屏,但在第三次泄漏后,对41.91-49.80米、53.80-61.68米所有管屏管子与鳍片根部进行打磨PT检查,鳍片边缘42根管子有裂纹。考虑到局域网对机组运行方式的安排,9月10日—10月13日,将未更换的鳍片管全部改为光管(TP347H),为了保
持管屏在炉内的刚度分别加装五层Φ76×6、长度100mm、材质为310S的套管,将套管焊接连成一个整体。